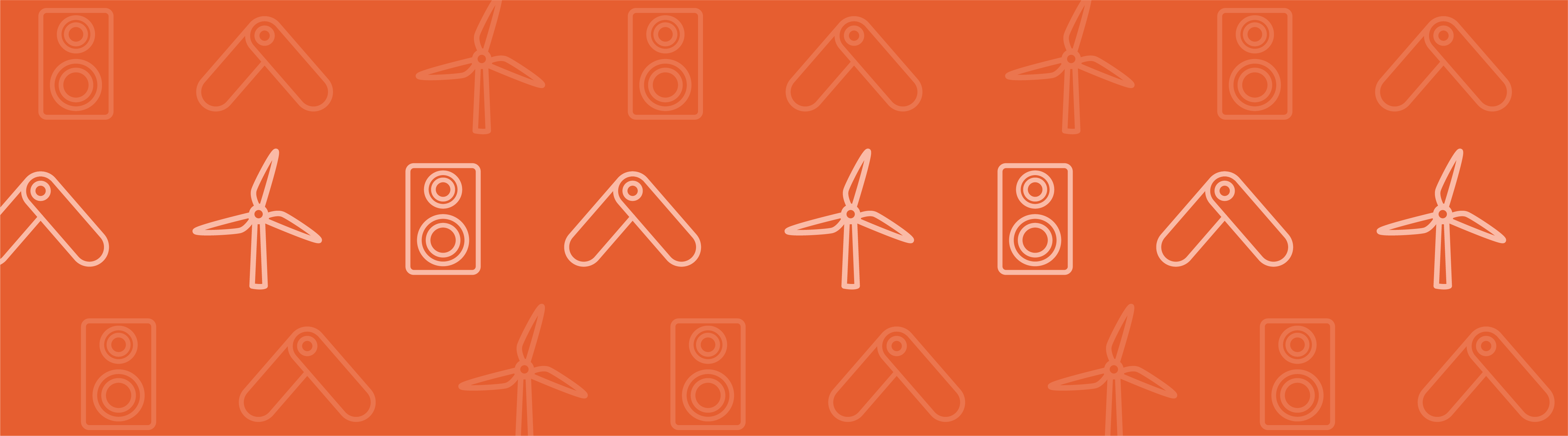
Engineers simulating fatigue in nonlinear materials are faced with two challenges. You must correctly represent the material behavior with a constitutive relation and find a fatigue model that captures the life-controlling mechanism. Both challenges require a thorough material knowledge. Today, we will address these challenges when modeling thermal fatigue in nonlinear materials.
Thermal Fatigue
The numerical simulation of applications containing the aforementioned challenges can be tackled using the Nonlinear Structural Materials Module, which provides a collection of predefined nonlinear material models, in combination with the Fatigue Module, which contains fatigue models for many different applications.
When the temperature changes, materials want to expand or contract. In applications consisting of several different parts, this thermal deformation will be constrained, since the thermal expansion coefficients differ between various materials. The situation is more challenging in the presence of nonlinear materials.
About Material Nonlinearity
Material nonlinearity implies that the deformation is not proportional to the loading. The nonlinearity of different materials can be roughly divided into reversible and irreversible nonlinearity. Reversible nonlinearity is also called elastic nonlinearity, which means that the strain state returns back to the initial state once the external load is back at its starting point.
Materials that exhibit irreversible nonlinearity can sustain permanent damage when loaded and will not return to the initial state upon unloading. An example of this phenomenon is shown in the figure below, where a surface mount resistor with a nonlinear solder material is subjected to a thermal cycle.
Displacement in a surface mount resistor at the end of a thermal load cycle. Blue color denotes zero displacement.
The material nonlinearity is a creep mechanism that deforms the material once it is subjected to a stress field — even when the stress field is held constant. Since the thermal expansion of the different parts of the surface mount resistor is non-uniform (greater in the printed circuit board on the bottom and smaller in the resistor on top), the assembly is stressed during a thermal load cycle.
Once the thermal load has reached the end of a load cycle, and returned to the initial temperature, a permanent deformation (creep strain) is left in the solder joints on both ends of the resistor. The permanent deformation in the solder joints prevents the remaining parts from returning to the initial state. You can see this in the figure where the resistor is compressed and bulges, while the printed circuit board is elongated.
Another type of material nonlinearity occurs when the permanent deformation only depends on the applied load and does not deform at a constant stress. This is called plasticity and can be demonstrated simply by bending a paper clip back and forth. If the applied force is too high, the paper clip will remain in a deformed state that does not change with time. A combination of plasticity and creep is called viscoplasticity and is yet another nonlinear material behavior.
Stable Load Cycle
Repeated loading and unloading can cause fatigue cracks. Before the fatigue life can be evaluated, you must obtain a stable load cycle. When working with nonlinear materials, many load cycles are often required before the material’s response stabilizes. Generally speaking, the nonlinear material response to a cyclic load can be summarized by three cases: immediate stability, shakedown, and ratcheting.
- In the case of the immediate stability, the second load cycle will already give a stable stress-strain response that is representative for each consecutive load cycle. This is demonstrated with the dotted black line in Case (a) in the figure below.
- At shakedown, the elongation stops first after a certain number of cycles. Therefore, a large number of cycles may need to be simulated. See Case (b).
- In ratcheting, Case (c), the material experiences a continuous elongation until failure. This case is the most challenging from a fatigue point of view since a stable load cycle is never obtained. In this case, you must generally simulate all cycles from initial state to failure.
Material response to a repeated load cycle: (a) immediate stability, (b) shakedown, and (c) ratcheting.
Fatigue Models for Nonlinear Materials
There is no universal model that predicts fatigue for all nonlinear materials, and many models have been proposed over time. In the 1950s, Coffin and Manson examined fatigue in metals and proposed an exponential relation between the fatigue life and the plastic strain for the low-cycle fatigue regime.
Following this pioneering work, many researchers proposed slightly modified models, where the plastic strain has been replaced with a different strain measure, such as creep strain, plastic shear strain, total shear strain, and others. Below, you can see a comparison between two strain measures (effective creep strain and the shear creep strain) in a surface mount resistor model, which was taken from our Model Gallery:
Development of the creep strain in a solder joint. Effective creep strain, to the left, and shear creep strain, to the right.
Both strain measures are highest at the interface between the solder and the resistor, which coincides with the position of a thermal fatigue crack in real applications.
For many applications, strain alone is not sufficient for fatigue predictions. Instead, energy might be more suitable since it combines the effect of stress and strain. In the 1960s, Morrow proposed an exponential relation between the fatigue life and the cyclic plastic strain energy. This model has later been modified to depend on other energy quantities, such as creep strain energy, total strain energy, stress-strain hysteresis energy, viscoplastic strain energy, and others.
Many times, the fatigue-controlling energy quantity is a nonstandard energy variable that requires a separate computation. This can be done in COMSOL Multiphysics, as demonstrated in the example of accelerated life testing, where the nonlinear material has two creep mechanisms. The first one controls strains at low stresses and the second one controls strains at high stresses. The fatigue, on the other hand, is controlled only by the energy dissipation caused by the creep development at high stresses.
The strain development as well as the energy dissipation by different mechanisms is calculated in individual distributed ODE interfaces:
Model set-up for evaluating user-defined creep strains and energies using ODE interfaces (to the left). A comparison of the results between the user-defined constitutive relations and the predefined material model from the Nonlinear Structural Materials Module (to the right). The green line is the dissipated energy at low stresses, the red line is the dissipated energy at high stresses, the dotted turquoise line is the combined dissipation by both mechanisms, and the blue line is the dissipated energy calculated with the material model from the Nonlinear Structural Materials Module.
Fatigue cracks are frequently encountered at interfaces of sharp geometrical changes and in corners. Those places are also well-known for causing numerical singularities. Thus, a point evaluation there can give misleading results.
Darveaux proposed a model that uses an energy volume average. This approach reduces the sensitivity to meshing in critical places and predicts life based on the surrounding state. In the figure below, we use the Darveaux model to predict fatigue life based on the dissipated viscoplastic strain energy in a ball grid array.
Fatigue life based on the average dissipated creep energy. All joints in two ball grid arrays are analyzed in a full model on the left-hand side, and to the right, a detailed study of the critical solder joint in a submodel is shown.
At first, all solder joints are analyzed in order to identify the critical one. Then, the critical joint is reanalyzed in a detailed study using a submodeling technique described in a previous blog post. The fatigue life in the thin layers at the interface with other materials, where cracking is expected, is finally predicted. Since the model evaluates a volume average, the results are calculated per domain.
We can evaluate the Coffin-Manson model with different strain options in the Strain-based fatigue feature. The Morrow and the Darveaux models with different energy options can be evaluated using the Energy-based fatigue feature.
Thermal Fatigue Examples
To wrap this up, I’d like to share a few examples where the thermal fatigue of nonlinear materials is simulated:
- The Thermal Fatigue of a Surface Mount Resistor model demonstrates how to perform a fatigue evaluation based on creep strain and the dissipated creep energy using the Coffin-Manson and Morrow type relations.
- In the Energy-Based Thermal Fatigue Prediction in a Ball Grid Array example, a microelectronic microchip containing several viscoplastic solder joints is analyzed. The fatigue life is based on the Darveaux energy volume average. This model also demonstrates how to analyze large models using the concept of submodeling.
- Fatigue life prediction, based on a more exotic energy and strain representation, is modeled in the Accelerated Life Testing example. Here, a material behavior with two creep mechanisms is evaluated and fatigue life, based on one mechanism, is predicted. The separation of strains in the two mechanisms requires recalculation of individual strains using separate ODE interfaces.
You can find all of these example models in the Fatigue Module Model Library.
If you are interested in learning more about fatigue modeling in nonlinear materials, join the Nonlinear Structural Materials Modeling and Fatigue Evaluation webinar on May 15th.
Comments (0)