Drag Reduction System in Motorsport
Application ID: 131731
Active aerodynamics systems actuate components on a vehicle dynamically to improve fuel efficiency, optimize cooling, and enhance stability. A drag reduction system (DRS) is an example of an active aerodynamic technology, which is often used in Formula 1® cars to overtake other cars during races. The core component of a DRS is an adjustable flap on the rear wing of the race car, which can lift to decrease aerodynamic drag and downforce, allowing the car to achieve higher speeds.
In this model, a 2D cross section of an airfoil is modeled to demonstrate the effect of an adjustable flap on drag and downforce. The moving flap is modeled using the Moving Mesh interface and fluid flow is modeled using the Turbulent Flow, k-ε interface. When the DRS is activated, it is observed that the drag coefficient decreases by up to 27.1% and the downforce decreases by up to 23.6%.
To learn more about this model, see our accompanying blog post "Modeling Drag Reduction Systems for Motorsports Using CFD".
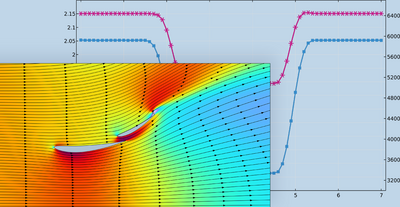
This model example illustrates applications of this type that would nominally be built using the following products:
however, additional products may be required to completely define and model it. Furthermore, this example may also be defined and modeled using components from the following product combinations:
The combination of COMSOL® products required to model your application depends on several factors and may include boundary conditions, material properties, physics interfaces, and part libraries. Particular functionality may be common to several products. To determine the right combination of products for your modeling needs, review the Specification Chart and make use of a free evaluation license. The COMSOL Sales and Support teams are available for answering any questions you may have regarding this.