Standing Contact Fatigue
Application ID: 35021
A standing contact fatigue test is a procedure used for testing crack growth on the subsurface level. In such a test, a spherical object is pressed against the tested materials and cycled between a high and low compressive load. No translational movement between the two occurs.
After a period of time, surface cracks can be observed on the flat object's surface, while further analysis of the component reveals multiple cracks that are present on the subsurface level. The surface is originally hardened, which changes the material properties of the surface in comparison to the material properties of the rest of the object. This surface hardening procedure affects the material strength, hardening, and fatigue properties of the object, while residual stresses are also introduced throughout the depth of the object.
Three distinct layers of fatigue-affected material can be observed. Closest to the surface, the specimen has a strong case layer, while in the core, the material has unaffected material properties. In between these layers, there is a transition layer where both the material properties and the residual stress have strong gradients. All of these effects are incorporated in the simulation of the load cycle.
In this example, fatigue is simulated using the Dang-Van model. The results show stresses that are a combination of the residual state from the hardening process and the structural response to the plastic deformation arising from the indentation of the spherical object. Plasticity occurs only during the first load cycle, while subsequent load cycles are elastic in nature. The second load cycle can therefore be seen as a stable load cycle and is used in the subsequent fatigue study.
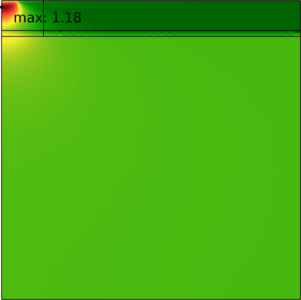
This model example illustrates applications of this type that would nominally be built using the following products:
however, additional products may be required to completely define and model it. Furthermore, this example may also be defined and modeled using components from the following product combinations:
- COMSOL Multiphysics® and
- Fatigue Module and
- Nonlinear Structural Materials Module and
- Structural Mechanics Module
The combination of COMSOL® products required to model your application depends on several factors and may include boundary conditions, material properties, physics interfaces, and part libraries. Particular functionality may be common to several products. To determine the right combination of products for your modeling needs, review the Specification Chart and make use of a free evaluation license. The COMSOL Sales and Support teams are available for answering any questions you may have regarding this.