Critical Temperature Control of Silicon Micro-Reactors for Lab-On-Chip Applications
The development of microfluidic components for implementation of a lab-on-chip system requires both fluid movements under a controlled environment as well as sensitive detection. This work involves the design and simulation of micro-reactors with integrated heating as well as optical detection facilities. Si micromachining was carried out using crystallographic etching techniques and micro-reactors in the form of inverted pyramids were developed. While this method limits the geometry of the reactor to those possible through preferential etching of crystallographic planes, it is low-cost, can generate high etching rates and automatically produces atomically smooth reactor sidewalls. Si material also allows the integration of driving circuit on-chip with the fluidic system. The dimensions of this reactor were 750 x 750 µm with side walls sloping at 54.70. At the bottom of the reactor there was an optical window 30x 30 µm wide. In order to carry out controlled reactions in the fluid phase within this micro-reactor it is necessary to create either a uniform temperature distribution or a specific temperature profile. This can be implemented using a microheater arrangement surrounding the exit aperture on the bottom face of the Si wafer. Design work was carried out using COMSOL Multiphysics®
3.5 and the microheater geometry was optimised for the abovementioned task. The design parameters were the height and depth of the Si based micro-reactor, the specific geometry of the microheater, thickness of the heating elements and the inter-element spacing. Several possible geometries were investigated in the design of the microheater, including a symmetric spiral as well as multi lobed spiral structure. Our result indicate that while uniform temperature can be achieved for planar structures using symmetric spiral microheaters, due to the shaped sidewalls of the micro-reactor, special considerations must be taken. Specifically since the Si sidewalls are wedge shaped, the distance from the heating element to the fluid surface is minimum near the aperture and increases gradually outward. Therefore the inter element spacing must be adjusted to account for this variation. The second consideration is the presence of corners as the reactor is not cylindrically symmetric but depends on crystallographic etched planes with well-define angles between them. The third consideration for the design was the limitation of the technology available for the task which restricted the smallest feature size. Optimised structures lead to a spatial variation of temperature to less than 20K. Such reactors when fabricated based on the optimised design are expected to play an important role in development of a microfluidic platform which can be used in diverse process and sensing requirements.
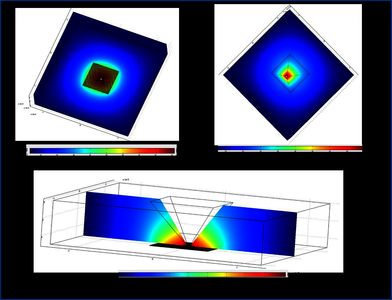