Investigation of Silicon Etching Process with COMSOL®
In this work we investigate a wet-chemical silicon etching process. COMSOL Multiphysics® is used to extract local pressure values to correlate them to experimental results. The test setup consists of a box with a fixed wafer and a nozzle that injects an etchant jet onto the wafer surface. We conduct experiments at different flow rates and fixed duration. Numerical process simulations in COMSOL Multiphysics® are used to elucidate the appearance of inhomogeneities at the etched surface. What are the dominating physical or chemical parameters that lead to different etching results? This modeling allows for the design of optimum geometries and flow velocities in this application. For the calculations in COMSOL Multiphysics®, the CFD module is used to calculate parameters such as flow velocity, (turbulent) kinetic energy, etc. and also the pressure. In order to validate the simulations, we compared them with results of an experimental study.
Experimental results
At the front of the wafer, the nozzle-facing side, parabolic light areas can be observed. With increasing flow rate, the parabolic area is getting wider. The observed parabolic shape on the wafer surface is very similar to the shape of the flow field in the simulations (figure 2, right side). In addition to the parabolic shape, an “imprint” of the nozzle is observed in the middle of the wafer, cf. Figure 3. The nozzle imprint can be divided into three different areas. An outer area with fine scratches (blue line), a white area (green line) and a grey area in the middle (red line). The diameter of the imprint increases with increasing flow velocity. Figure 3 shows the calculated pressure curve for an experiment in good agreement to the experiment.
In the final paper we will extract the simulated pressure values at the edge of the three regions of the imprint for all experiments of the study. We will test if consistent values can be determined from the different simulations and experiments so that we can correlate the local pressure to the etched surface quality.
Conclusions
The experimental observations led to the conclusion that the pressure might be a decisive parameter for the etching behavior. We used COMSOL CFD simulations to extract the local pressure for different etching parameters and model the silicon etching process to test this hypothesis.
Acknowledgement This work was funded by the German Federal Ministry for Economic Affairs and Energy under contract number ZF4098906ZG6.
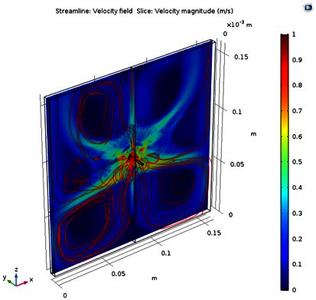
Download
- kray_poster.pdf - 1.29MB
- kray_abstract.pdf - 0.3MB