Modeling and Simulation of Porous Silicon Membrane based Fuel Cell
Miniature hydrogen fuel cell based on porous silicon has the potential to power miniature electronics more efficiently as it might be easier for it to be integrated on a silicon chip. In such fuel cell, porous silicon acts as proton conducting membrane, Pt layer over porous silicon as anode catalyst and Si substrate over which porous silicon is formed as cathode. The thickness of anode catalyst decides the rate of oxidation reaction, thickness and porosity of porous silicon controls rate of proton exchange between anode and cathode and thickness of cathode not only decides rate of reduction reaction but also bulk resistance. Each layer has to be of optimum thickness to obtain good open circuit voltage and current density from such fuel cell. Other researchers have reported open circuit voltage of 450 mV from such fuel cell [1-3]. In the present work we have obtained open circuit voltage of 1.1 V and current densities upto 700mA/cm2 from such fuel cell. Fuel cell model from the COMSOL® application library was used and material, physics, and properties of the model were modified to mimic our fuel cell device. We have run multiple simulations in COMSOL® by varying parameters like anode thickness, membrane thickness, cathode thickness, H2 gas mass flow rate and O2 gas mass flow rate to find optimum parameters that may lead to the fabrication of good performance fuel cell.
In our present work through simulation we found that anode catalyst thickness to be kept at 300 nm, porous silicon membrane thickness to be kept between 20-100 µm, cathode catalyst thickness to be 200 µm and H2 and O2 gas flow mass fraction in the ratio of 0.8:0.6. With these parameters such fuel cell provided open circuit voltage upto 1.1 V and current density upto 700 mA/cm2.
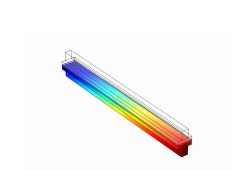
Download
- agarwal_poster.pdf - 0.36MB
- agarwal_abstract.pdf - 0.1MB