Multiphysics Analysis of a High Power RF Window using COMSOL Multiphysics®
The design and analysis of a multidimensional system involving multiphysics considerations requires solving of complex equations. A high power continuous wave RF component is one such system. The poster reports the design, multiphysics analysis, low and high power experimental results of a high power RF window. The RF window is a mechanical isolation between Ultra High Vacuum (UHV) and pressurized sections of a system. However, it ensures a very high return loss and low insertion loss. It is a rectangular to circular converted waveguide with a dielectric disc brazed at the centre of the circular waveguide which is transformed back to rectangular waveguide. This is well illustrated in Figure 1. The design and analysis of the 3.7 GHz, 150 kW window involves RF characterization of the design, thermal analysis, cooling considerations and stress analysis. These analyses were performed using the RF, Heat Transfer, Structural Mechanics and CFD modules of COMSOL Multiphysics®. The window comprises of a dielectric disc shaped material which was modeled using the Wave electric node of the Electromagnetic RF module at 3.7 GHz. The window provided a return loss ~55 dB and an insertion loss of ~0.01 dB. The dielectric material results in volumetric losses while the enveloping copper causes surface losses which act as RF load for the Heat transfer module to be used later. The window is subjected to high power for long durations and results in radiation from dielectric to vacuum, conduction from dielectric to enveloping copper and convection from copper to atmosphere. The Heat transfer module considers all the RF loads and the thermal issues. The heat load obtained is used as an input to the Solid mechanics module which suggests heavy deformation in the structure due to the high temperature gradients. The CFD module is thus used with some cooling arrangements in the structure to reduce the overall average temperature of the structure. This allows continuous use of the window with deformations within the acceptable limits. Post cooling the peak temperature rise obtained was ~0.5°C. The window was fabricated using high temperature vacuum brazing and was subjected to low power RF characterization using Vector Network Analyzer (VNA). The RF characterization conforms the COMSOL Multiphysics® simulation results. Also, the window is subjected to 3.7 GHz, 150 kW RF power and its performance is acceptable and in very good agreement with the COMSOL Multiphysics® simulation results.
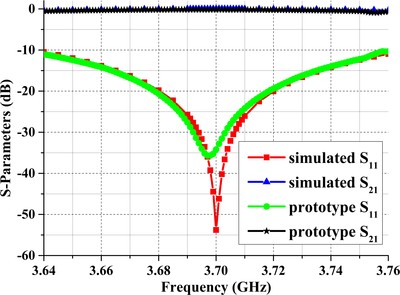
Download
- Bangalore_2019_Yogesh_Jain_presentation.pdf - 1.49MB
- Bangalore_2019_Yogesh_Jain.pdf - 1.35MB