Thermomechanical Modeling of Dislocation Density Increase During PVT of SiC Crystals
During Physical Vapor Transport (PVT) growth of single 4H-SiC crystal and subsequent cooling down, thermal stresses lead to the multiplication of dislocations that are non-desirable for the semiconductor applications of this material. These dislocations induced by thermal stresses could be reduced by an appropriate control of the thermal gradients inside du crystal during its growth and cooling down [1,2]. A thermomechanical modeling able to predict the formation of dislocations in the crystal would thus be of great interest to optimize the PVT process.
The objective of this study was to use COMSOL Multiphysics® software to develop a thermomechanical approach using the Alexander-Haasen (AH) model to estimate the amount of dislocations created during crystal growth and cooling down. To model the formation of dislocations the AH model uses a plastic strain rate that is a function of the stress tensor and of an internal variable, the density of mobile dislocation Nm. The evolution rate of Nm is also function of the stress tensor which adds an Ordinary Differential Equation (ODE) to the problem [3,4]. Coupling between this additional domain ODE and creep/viscoplastic user-defined non-linear structural material behavior law has been successfully set up within COMSOL Multiphysics.
First, an uniaxial compression test is used to validate the model and adjust the model parameters to experimental data. Then, the cooling down of cylindrical crystals is studied, in particular the influence on the dislocation density increase of the direction of the thermal gradient and the crystal size (Fig. 1&2). A real case, using an actual PVT reactor geometry for heat transfer computation and a crystal geometry coming from a thermo-chemical computation [5] is also treated (Fig. 3). For the sake of simplicity, axisymmetry is used and only the cooling down has been addressed. Indeed, during crystal growth the evolution of geometry and boundaries complicate the problem. However, some initial trials of thermomechanical modeling during growth are presented as perspectives of this work, as well as 3D simulations (Fig. 4).
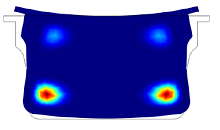
Download
- jauffres_presentation.pdf - 2.99MB
- jauffres_abstract.pdf - 0.02MB