To a Fluidic Diode for Biomedical Application
This work is focused on Micropump optimization for drug delivery application. Diabetes is one of the widely pervaded diseases. Among the side effects of hyperglycemia is the weakness of the whole body, so the patient will be unable to inject manually the drug. Therefore, Micropumps are fabricated to automatically and safely inject insulin to the patient. Micropumps designed with valves are not desirable because of their reciprocating movement which makes them weaker and breakable. This risk can be eliminated using Diffuser/Nozzle structures that do not contain any moving parts, and then the reliability is enhanced. Although such design enhances the lifetime of these biomedical Micropumps, it is essential to reduce the backflow of the liquid to make them efficient. Here we focused on the planar Diffuser/Nozzle geometry in purpose of having more important flowrate in the diffuser direction rather than in Nozzle direction. The non-desirable backflow is limited through optimizing the different Diffuser/Nozzle parameters (Neck width, Diffuser length, Opening angle, …) (figure 1). The Diffuser/Nozzle is modeled and simulated using COMSOL Multiphysics® under the Laminar Flow physics interface. Here, the necessary parameters results are visualised (Fluid Velocity, Pressure Loss, Flowrate) and compared with the new structure of Diffuser/Nozzle for different geometry dimensions. The backflow is then reduced which allows to enhance the Micropump reliability. A prototype of the new Diffuser/Nozzle structure is under micromachining using 3D printer and it will be used to verify modeling results with experimental data. In further work, the integration of this new Diffuser/Nozzle structure into the biomedical Micropump will be treated under COMSOL Multiphysics®.
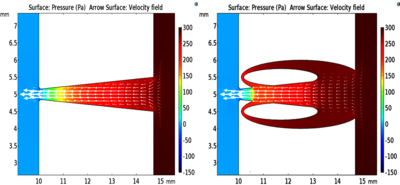
Download
- leoni_poster.pdf - 1.27MB
- leoni_abstract.pdf - 0.09MB