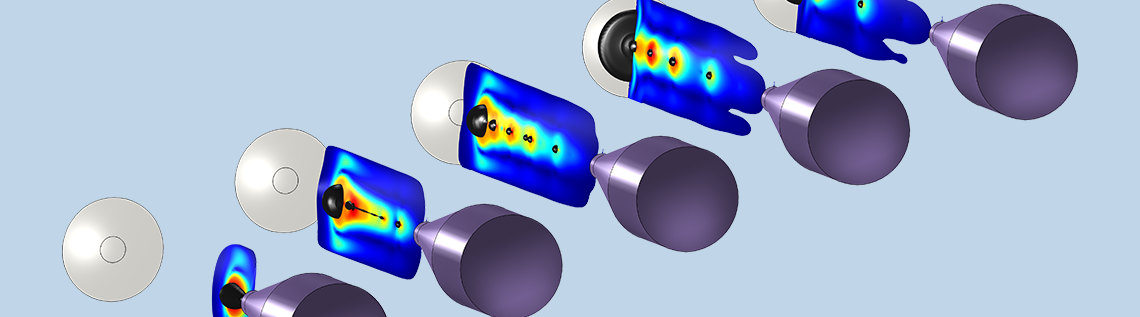
If an inkjet printhead nozzle is poorly designed, it will lead to a low-quality end product — whether it’s used in a 2D or 3D printer, the fabrication of an integrated circuit, or even DNA synthesis. With simulation, you can determine the ideal printhead nozzle dimensions to achieve precise material deposition. And with the COMSOL Multiphysics® simulation software, you can save time by turning your model into an app for use by other project stakeholders.
The Inkjet Printhead Nozzle: A Key Component in a Variety of Applications
Inkjet printers are widely used to provide high-resolution 2D printouts of digital images and text, where the printhead ejects small droplets of liquid from a nozzle onto a sheet of paper in a specific pattern. In addition to printing images onto paper, the inkjet technique is also common in 3D printing processes. The printhead moves over a certain type of powdered printing material and deposits a liquid through the nozzle onto the powder to effectively bind it into a predetermined 3D shape. (Tip: Check out the video on 3dprinting.com to see this process in action.) Inkjet printheads are also prevalent in life science applications for diagnosis, analysis, and drug discovery. The nozzles are used as part of a larger instrument to deposit microdroplets in a very precise fashion.
An inkjet nozzle deposits an ink droplet, which travels through the air before reaching its target. The model was created using the COMSOL Multiphysics® software.
No matter what device or machine relies on the inkjet printhead to deposit material, precision is crucial. Therefore, the quality of the end product hinges on the nozzle design.
Studying the Fluid Flow in an Inkjet Nozzle with Simulation
The droplet size for an inkjet nozzle is a key design parameter. In order to produce the desired size, you need to optimize the design of the nozzle and the inkjet’s operating conditions. Rather than build nozzle prototypes and test them in a lab, you can use simulation software to understand the physics of the fluid ejection and determine the optimal design. COMSOL Multiphysics® is one such software package.
When you expand COMSOL Multiphysics with either the CFD or Microfluidics add-on module, you can create models that help you understand how the ink properties and nozzle pressure profile affect the droplet velocity and volume as well as the presence of satellite droplets.
Model created using the level set method to track the interface between air and ink. The color plot around the droplet signifies the velocity magnitude in the air.
What happens inside the inkjet nozzle when the liquid is emitted? First, the nozzle fills with fluid. Next, as more fluid enters the nozzle, the existing fluid is forced out of the nozzle. Finally, the injection is halted, which ultimately causes a droplet of liquid to “snap off”. Thanks to the force transmitted to the droplet by the fluid in the nozzle, it travels through the air until it reaches its target. In terms of physics, inside the nozzle, there is a single-phase fluid flow. When the liquid moves through the air, the flow becomes a two-phase flow.
We won’t go into the details of how to build this model here, because you can download the step-by-step instructions in the Application Gallery.
As the simulation specialist in your organization, you are a member of a small and rather exclusive group of people tasked with serving a larger pool of colleagues and customers who rely on your models to make important business and design decisions. Wouldn’t it be nice if these stakeholders could take on some of the work that goes into rerunning simulations for different parameter changes?
Save Time by Building Apps Based on Your Model
The COMSOL Multiphysics software comes with the built-in Application Builder, which enables you to wrap your sophisticated models in custom user interfaces. By building your own apps, you can give your colleagues or customers access to certain aspects of your models, while hiding other aspects that may be unnecessary to change and too complicated to expose. For example, suppose that your colleagues in design or manufacturing want to test the performance of an inkjet nozzle for different geometries and liquid properties. Instead of coming back to you each time they want a minor change to the underlying model, they can input different values in simple fields and click on a button to plot new simulation results in the app you provide them. Since they can run their own analyses, your time can be spent on new projects, models, and apps.
To show you what we mean — and to inspire you to make your own apps — we have made a demo app based on our inkjet tutorial model. In this example, the app user can analyze various nozzle designs to see which version produces the ideal droplet size. Contact angle, surface tension, viscosity, and liquid density are all taken into account in the app. As you can see in the screenshot below, an app user can adapt the nozzle shape and operation by changing different input parameters.
An example of what an inkjet printhead design app might look like. In this demo app, users can modify liquid properties, the model geometry, and simulation time intervals.
When you build apps, you can empower other stakeholders to make better decisions faster without actually giving them access to your full underlying model. The model simply powers the app and you, as the app designer, decide what inputs the users can modify. Your original model file stays safely untouched in your care, but a variety of results are accessible by those who rely on them most.
Try It Yourself
Get started by downloading the .mph file and accompanying documentation for the tutorial model and demo app from the Application Gallery.
All you need to download the documentation is a COMSOL Access account. To get the .mph file, you will also need a valid COMSOL Multiphysics® software license or trial. Note that you can access these files directly within the product as well, via the Application Libraries.
Other Related Resources
- Watch a keynote video on industrial inkjet printheads from the COMSOL Conference 2014
- Get an introduction to modeling separated three-phase flow with COMSOL Multiphysics
- Learn about modeling piezoelectric actuators
Comments (1)
Clarence Velez
August 29, 2021Hi
Thanks for this helpful blog. Please consider simulating a real printer which after falling of droplet and hitting the target then it solidifies. Is it possible to simulate such a problem in COMSOL and how?