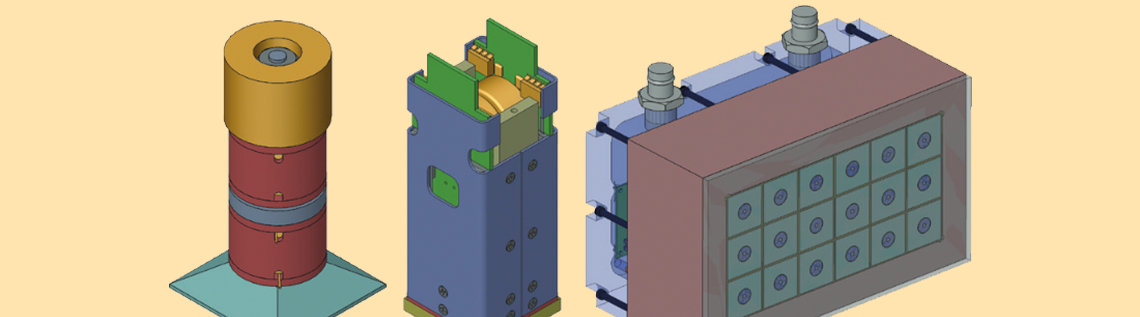
The magnetostrictive effect causes magnetic materials to change their shape when a magnetic field is applied. Materials that exhibit such behavior are used in a range of devices, from loudspeakers to actuators. In order to analyze one type of device, a magnetostrictive transducer, researchers from ETREMA Products, Inc. performed single-physics and multiphysics simulation studies in COMSOL Multiphysics. See how the flexible nature of the software enabled the team to study various aspects of the device and optimize its overall design.
A Short Introduction to Magnetostriction
The magnetostrictive effect is fairly common; in fact, you may have heard this effect in action before. Familiar with the humming sound that comes from a transformer or other high-powered electrical devices? At the root of this magnetic hum is magnetostriction.
To better understand magnetostriction, we can begin by taking a closer look at magnetostrictive materials. When exposed to a magnetic field, the tiny ellipsoidal magnets inside magnetostrictive materials realign themselves, as shown in the animation below. This new order results in a macroscopic strain, causing the solid material to stretch or shrink. As such, magnetostriction can be used to convert magnetic energy into kinetic energy. The opposite effect is also possible, as applying stress to a magnetostrictive material can change the material’s magnetic state.
An animation illustrating magnetostriction.
Using Simulation to Analyze Magnetostrictive Materials
Engineers at ETREMA Products, Inc. have experience working with magnetostrictive materials. Using smart materials with magnetostrictive behavior, they design high-precision devices like sensors, loudspeakers, actuators, and SONAR components. Because smart materials respond to external stimuli in different ways, their design can be based on where they will be used and for what purposes. A magnetostrictive material represents a specific type of smart material, one that responds to a magnetic field by changing its shape.
A magnetostrictive transducer. Copyright © ETREMA.
Terfenol-D, of which ETREMA is the only commercial manufacturer, is one example of a magnetostrictive material. First developed in the 1970s by the U.S. Navy, Terfenol-D responds to an applied magnetic field with the largest deformation of any alloy. At ETREMA, this material has proven to be a powerful resource in magnetostrictive transducer design. However, due to the nonlinearity of magnetostrictive materials and because they respond mechanically to changes in magnetic fields, designing these devices can be rather challenging. To address such challenges, a team at ETREMA turned to multiphysics simulation, accurately developing models that include several components, custom-defined materials, and multiple types of physics.
The simulation study that they conducted involved two steps. The first step was designed to provide a narrow view that analyzes individual physics. The goal here was to generate a targeted analysis of the design, enabling the engineers to easily evaluate specific physics. The second step was designed to provide an overarching view that analyzes multiple physics. In this case, the team wanted to find out how their design would work in a realistic setting by investigating its overall functionality.
Optimizing a Magnetostrictive Transducer
As an example, let’s take a look at their closely packed SONAR source array design, which features a magnetostrictive transducer at its core. Optimizing this device prompted the need for studying its various material properties, as well as interactions between the electrical, magnetic, and structural physics.
Images showing the components of a closely packed SONAR array. Left: The magnetostrictive transducer. Center: The transducer and power electronics. Right: The full array. Copyright © ETREMA.
The team began their study by looking at deformation using a single-physics model. The initial study involved applying static loads to estimate fatigue in order to predict how the Terfenol-D core and prestressed bolts would react to system strain. This configuration showed severe bending between the transducer and the load. Further load analyses and structural optimization, however, facilitated the design of a transducer with reduced deformation and stress.
Deformation in the initial transducer design (left) and the optimized configuration (right). Copyright © ETREMA.
Another simulation study focused on the magnetic fields of the device. When developing their magnetostrictive transducer, the team of engineers added permanent magnets to the design. While this enabled them to magnetically bias the material to allow for bidirectional motion, as well as minimize nonlinear behavior and frequency-doubling effects, it was not without negative effects. Case in point: Noise problems and corrupted signals can result from stray magnetic fields that are too close to the transducer’s electronics. In an effort to avoid this, separate studies were performed for DC and AC magnetics, with the design and placement of the magnetic circuit and important electrical components also evaluated.
Looking over their simulation results, the team observed that the magnetic fields within their design stayed mostly confined to magnetic components, reducing the exposure of the electronics to the magnetic field. These results empowered the development of a magnetostrictive transducer that was optimized for the competing AC and DC magnetic requirements.
Elaborating on their single-physics models, engineers at ETREMA then used multiphysics models for design validation. This is a crucial step, as transducer technologies are focused on magnetostrictive materials, which include multiple physics. Setting up these models involved using coupled equations where strain is a function of stress and the magnetic field.
The coupled model was used to investigate the device’s deformation, with regards to mechanical stress and magnetic fields as well as its overall electromechanical characteristics. These simulation studies provided a more accurate prediction of how the design would behave in the real world.
Coupled simulation showing the magnetic fields caused by a 1-ampere input to the coil, with displacements calculated using the maximum current input. Copyright © ETREMA.
With their coupled linear magnetostrictive model, the team found that their device performed mostly as expected, with only a few adjustments needed. Additionally, they observed that the magnetic fields were still confined to the magnetic circuit and that deformations remained minimal. These findings were later validated by experimental data.
The simulation studies presented here showcase the flexibility of COMSOL Multiphysics and how the software can be used to analyze many different aspects of a design. In this case, engineers at ETREMA were able to develop, analyze, and optimize transducers by using both single-physics and multiphysics models. Such research has improved their knowledge of transducers and transducer designs, fostering further advancement within this field.
Find Out More About the Role of Simulation in Studying Magnetostrictive Materials
- Want to learn more about ETREMA’s use of multiphysics simulation? Browse these resources:
- Read a related article: “Making Smart Materials Smarter with Multiphysics Simulation“
- Watch a conference keynote presentation from Julie Slaughter about modeling magnetostrictive transducers
- See this blog post for more details on modeling magnetostriction in COMSOL Multiphysics
Comments (3)
David Xu
April 5, 2019Can the company provide simulation service?
We have a need for simulation stress/strain-magnetization of defects in carbon steel pipe–a natural gas pipeline industry project.
David
dxx2@pge.com
ANJALY KRISHNA SAI
April 25, 2019Hii
Can you tell me how to capture magnetostriction on Induction Motor stator?
Brianne Christopher
April 26, 2019 COMSOL EmployeeHello Anjaly,
Thank you for your comment.
For questions related to your modeling, please contact our Support team.
Online Support Center: https://www.comsol.com/support
Email: support@comsol.com