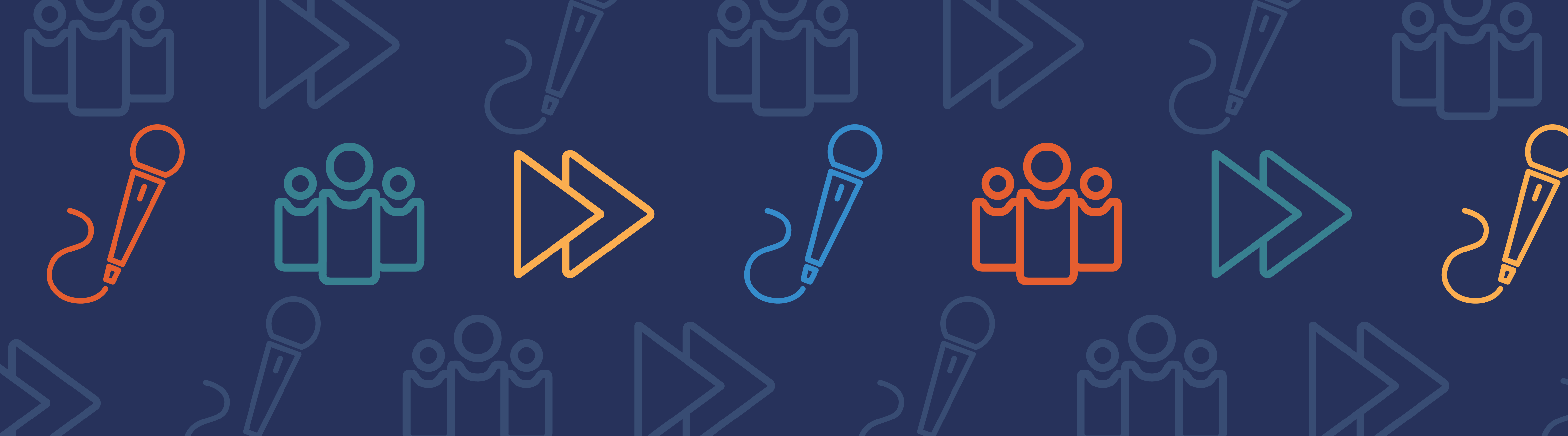
How can simulation applications strengthen the relationship between companies and their customers? In his keynote presentation from the COMSOL Conference 2018 Lausanne, Florian Klunker from Huntsman Advanced Materials discussed providing simulation as a service to customers. Deploying applications via the COMSOL Server™ product helps users efficiently learn about and develop processes, enabling simulation experts to focus on innovation. If you missed his talk, you can watch a recording of the video and read a summary below.
Florian Klunker Discusses Providing Simulation as a Service to Customers
Meeting Product Quality Standards by Enhancing Process Understanding
Huntsman Corporation manufactures a wide range of specialty chemicals. Huntsman has four different divisions (polyurethanes, performance products, textile effects, and advanced materials) and over 10,000 employees worldwide.
Florian Klunker is from Huntsman Advanced Materials. To support industries such as automotive, aerospace, composites, and more, they’re always advancing their research and development. Although these industries provide different challenges, one thing these industries have in common is that process simulation is a useful tool to support them.
There are three main steps to process simulation at Huntsman Advanced Materials:
- Experiments, such as dynamic scanning calorimetry and rheology
- Material modeling by data fitting
- Finite element method (FEA) analysis, such as cure and flow simulations
Florian Klunker said that their researchers have a long history of using process simulation with resin casting, for example, which is often used as an insulator for power applications. Simulation helps his team to support customers and the product development by determining the optimal resin systems.
Benefits of Applications for Colleagues, Customers, and Simulation Experts
Rather than trying to make a perfect model, Florian Klunker said that he and his group use simulation as a “GPS,” which serves as a guideline for meeting their goals as fast as possible. Afterward, they figure out the more specific details together with their customers on-site. By taking this approach, they can optimize production, minimize resin curing time, as well as identify processing issues and propose alternatives.
What’s more, COMSOL Server™ helps Huntsman amplify the impact of the work of their simulation group. “Any model I do, I can transform into an [application] and share it with my colleagues,” said Florian Klunker. He gave an example of an application that included only a couple of buttons: one labeled “compare resins” and another called “compute.” Simply by selecting among three resins to compare, inputting the temperature and time for the reaction, and clicking compute, users of this application can get the reaction curves for the different resins as a function of time. Klunker said that these “few-click” simulations are an easy introduction to simulation for new users and that the integrated database helps applications stay updated.
Empowering Colleagues
An advantage of deploying simulation applications at such a large company is being able to reduce the maintenance effort for IT as much as possible. By making this tool available via a browser, it allows for web access without any local machine installations. Today, 75 employees within Florian Klunker’s division have access to such tools, allowing them to see the benefits of simulation firsthand. For example, it can help users to learn more about processes and improve them. With an application, Florian Klunker’s colleagues can identify key parameters and visualize their impact, which helps them determine the best materials and provide process solutions to their customers.
The solution is more and more accepted as the colleagues can see benefits like increased efficiency. For instance, because they have this virtual experimental platform, they can do fewer trials. In addition, the applications are designed to have a templated output, which allows for quick and unified reporting. What’s more, these simulation applications empower the colleagues to get the answers they need in a short amount of time, meaning that they can streamline their workflow and don’t need to wait for feedback from the simulation experts.
Empowering Simulation Experts
Because applications enable others to find answers and solutions themselves, simulation groups are able to focus more on innovation, such as by coming up with new processes or specialized models. In one example, Florian Klunker said that they developed a flow simulation to adapt the reactivity of resin during injection, allowing for faster curing. In a second example, he showed a simulation of dynamic fluid compression molding. Here, the challenge was to drive the process to the physical limits (mainly the heat transfer), and modeling helped to understand where these limits were.
From the video: Klunker discusses how simulation applications help promote innovation.
Simulation experts can also focus on the development of new materials. For instance, Huntsman now produces MIRALON™ materials, which represent a new class of advanced carbon-based performance material. The material structure is available in four different formats: sheets, tapes, yarns, and dispersions. Simulation is helping them to understand how the material can be used.
By deploying and distributing tools for process simulation, Huntsman Advanced Materials is able to predict manufacturing variability and account for processing flaws, answer common customer questions, and accelerate innovation and product development.
You can learn more about how Huntsman Advanced Materials uses COMSOL Server™ to provide simulation as a service to customers by watching the video at the top of this post.
Miralon is a registered trademark of Nanocomp Technologies, Inc.
Comments (0)