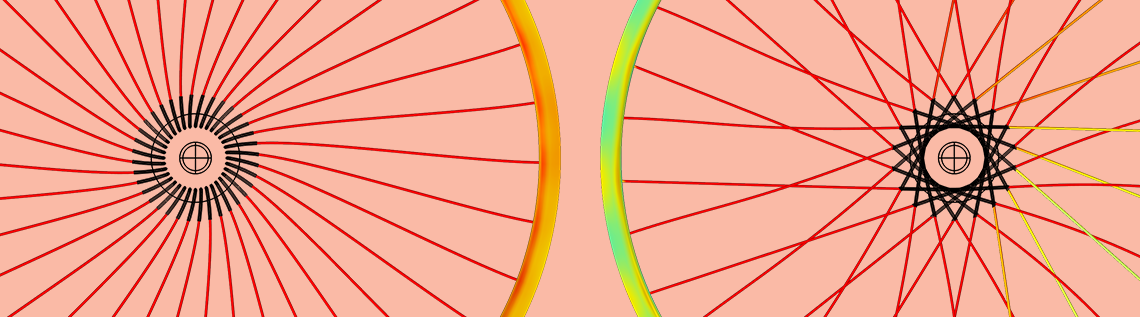
Bicycle brakes can be divided into two categories: rim brakes and hub brakes (including disc brakes). The different brake types cause different forces in the rim of the wheel, and the spoke lacing also plays a role. In this blog post, we will compute the stress in the rim for two types of brakes and two types of spoke lacing. It turns out that radial lacing of spokes with hub brakes is a bad combination.
Introduction to Brakes, Rims, and Spoke Patterns
Have you ever noticed that the rear wheel of a bicycle is never radially laced? Alternatively, you might have seen that the front wheel of the Tour de France bikes looks different after the transition to disc brakes. The reason why is the same: The torque from pedaling and braking requires a tangentially laced wheel to avoid excessive forces in the wheel rim. These forces do not occur for rim brakes because the whole wheel works as an arch without any torque on the wheel hub. This allows the rim to be lighter, thus explaining why some rims come with a warning: “Rim brakes only!”
A typical triathlon bike from 2005, showing the radial spoke layout characteristic of high-performance racing bikes at the time. Image by GS, reworked by אx — Own work. Licensed under CC BY-SA 3.0, via Wikimedia Commons.
Note that disc brakes were banned by the UCI before 2018, and that the change was not without controversy. Let’s take a look at how big the difference is in terms of structural mechanics…
Modeling the Forces in a Bicycle Rim
Here, we discuss the Modeling the Forces in a Bicycle Rim model, which uses the Design Module and the Structural Mechanics Module, both add-on products to the COMSOL Multiphysics® software.
The rim and hub are considered to be made of aluminum, while the spokes are made of structural steel. The tire pressure is set to 3 bar, and the Bolt Pretension feature is used to impose a spoke tension of 1 kN. Geometric nonlinearity is considered, and this makes the model quite nonlinear, so continuation in the load forces is applied. The two types of brakes are implemented as separate load cases, while the spoke lacing pattern is controlled with a parameter. Besides the four cases given by the lacing and brake type, we compute the effect of the braking force.
Simulation Results
The graph shows the average stress in the rim for the two load cases and geometries. The case with radial spoke lacing and disc brakes stands out as having larger stress. This explains why it is unsafe to use a rim designed for rim brakes with disc brakes.
Disc brakes give rise to higher rim forces, which can lead to wheel buckling for tangentially laced wheels.
In the case of radial spokes, a reorientation of the spoke forces is necessary to achieve torque balance on the hub. This is what causes the high rim forces for the disc brake as seen in the figure below. The stress is significantly below material yield stress, but it might still be enough to cause buckling failure.
The rim stress (rainbow color table) is plotted for a disc brake. Note how the rim rotates relative to the hub in the case of the radial spokes (right).
Catastrophic failure of the rim is one aspect, but stiffness can also play an important role in terms of maintaining control of the bike. The graph below shows the rotation of the rim relative to the hub for the two lacing- and brake types. The rim brake gives rise to marginal rotation of the rim, while the disc brake on a radially laced wheel causes large deformation.
The rim rotation mainly depends on the wheel lacing and brake type (note the logarithmic axis for the angle).
Summary
We have modeled the forces in a bicycle rim for different brake types and spoke lacing. The results explain why some rims come with warnings, and they also shed light on why some people still swear by rim brakes.
A less controversial subject is pedals. They tend to stay on, but do you know why? If not, you might be interested in one of our older blog posts: How Do Bicycle Pedals Stay On?
Next Steps
Try the Modeling the Forces in a Bicycle Rim model discussed in this blog post by clicking the button below:
Comments (2)
Ivar KJELBERG
October 19, 2021Hello,
Thanks for the interesting Blog, one comment, is it possible to propose (systematically) also a “reduced size – unsolved” and compacted MPH model files, as mostly the full size files are so big that for me, the download times counts in hours, we are not all linked to a fibre or have internet on “intravenous” mode 🙂
Sincerely, Ivar
Kristian Ejlebjærg Jensen
October 19, 2021 COMSOL EmployeeHello,
We have uploaded a compacted version of the MPH model file, but keep in mind that the model requires a machine with around 32 GB memory to solve.
best regards,
Kristian E. Jensen