Stress and Modal Analysis of a Composite Wheel Rim
Application ID: 78281
Nowadays, there is a trend to manufacture wheel rim made up of a composite material instead of aluminum. The primary reason is to have lower values of unsprung mass which leads to faster response time and thus better acceleration, braking and cornering performances. Typically a carbon fiber reinforced polymer (CFRP) composite is used to manufacture a composite wheel rim.
To understand and improve the design of a composite wheel rim, an example model is built in COMSOL. The example demonstrates the modeling of a wheel rim made up of laminated composite with carbon-epoxy material. The composite laminate has different number of plies in different regions of the wheel rim. First, a stress analysis of the wheel rim is performed in which rim is subjected to the inflation pressure and the tire load. In order to compute modal response of the wheel rim, a prestressed eigenfrequency analysis is performed in which rim is subjected to the rotating frame forces.
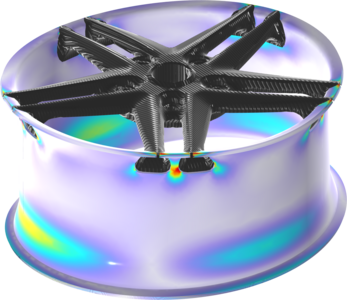
This model example illustrates applications of this type that would nominally be built using the following products:
however, additional products may be required to completely define and model it. Furthermore, this example may also be defined and modeled using components from the following product combinations:
The combination of COMSOL® products required to model your application depends on several factors and may include boundary conditions, material properties, physics interfaces, and part libraries. Particular functionality may be common to several products. To determine the right combination of products for your modeling needs, review the Specification Chart and make use of a free evaluation license. The COMSOL Sales and Support teams are available for answering any questions you may have regarding this.