Energy-Based Thermal Fatigue Prediction in a Ball Grid Array
Application ID: 16143
In a cooling system, a microelectronic component has been identified as the critical link. Since the power is repeatedly switched on and off, the component is subjected to thermal cycling. As a results a crack grows through a solder joint and disconnects the chip from the printed circuit board so that the component loses its operational functionality. The lifetime of the solder joints in two ball grid assemblies is predicted based on the Darveaux energy-based model. The fatigue model evaluates damage based on an averaged energy dissipation density in a thin layer where a crack will grow.
This example is based on a model from the Nonlinear Structural Materials Module, Viscoplastic Creep in Solder Joints. Since the model contains several solder joints that are modeled with a viscoplastic material, many degrees of freedom are required in order to simulate the correct creep behavior in all elements. From the fatigue point of view, only the critical part of the model is of interest. In order to capture it, the concept of submodeling is used. This technique requires two steps. In the first one, the full model is analyzed with a coarse mesh in order to simulate the general trends and to identify the critical solder ball. In the second step a submodel with a fine mesh containing the critical part is made and the study is recomputed. The global effects from the full model are transferred to the submodel via appropriate boundary conditions.
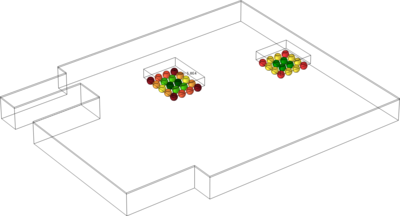
This model example illustrates applications of this type that would nominally be built using the following products:
however, additional products may be required to completely define and model it. Furthermore, this example may also be defined and modeled using components from the following product combinations:
The combination of COMSOL® products required to model your application depends on several factors and may include boundary conditions, material properties, physics interfaces, and part libraries. Particular functionality may be common to several products. To determine the right combination of products for your modeling needs, review the Specification Chart and make use of a free evaluation license. The COMSOL Sales and Support teams are available for answering any questions you may have regarding this.