Material Characteristics of a Laminated Composite Shell
Application ID: 67691
This model serves the purpose of validation and verification of the Linear Elastic Material, Layered model in the Shell interface. In COMSOL Multiphysics, composites are analyzed either based on Layerwise 3D elasticity theory through the Layered Shell interface or based on FSDT-ESL theory through the Shell interface.
The First Order Shear Deformation Theory (FSDT-ESL) is implemented in the Linear Elastic Material, Layered model in the Shell interface available with the Composite Materials Module. This theory treats a heterogeneous laminated composite as a statically equivalent single layer. ESL theory reduces a 3D continuum problem to an equivalent 2D problem, thus reducing the size and computational time of the problem.
This example is a NAFEMS benchmark, described in Benchmarks for Membrane and Bending Analysis of Laminated Shells, Part 2: Stiffness Matrix and Thermal Characteristics. Membrane and bending stiffness, flexibility matrices, midplane strains in case of unit loading, and the response to a unit change in temperature are verified.
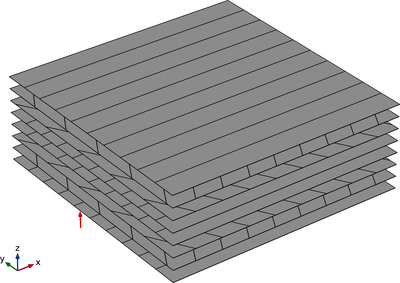
This model example illustrates applications of this type that would nominally be built using the following products:
however, additional products may be required to completely define and model it. Furthermore, this example may also be defined and modeled using components from the following product combinations:
The combination of COMSOL® products required to model your application depends on several factors and may include boundary conditions, material properties, physics interfaces, and part libraries. Particular functionality may be common to several products. To determine the right combination of products for your modeling needs, review the Specification Chart and make use of a free evaluation license. The COMSOL Sales and Support teams are available for answering any questions you may have regarding this.