Photoresist Spin Coating Simulation
Application ID: 121451
In the semiconductor manufacturing process, photoresist coating is an important process and the thickness of the photoresist layer needs to be precisely controlled. Usually, the photoresist layer is thinned by spin coating. The specific principle is to use centrifugal force to throw excess photoresist away from the wafer surface and generate a specific thickness of photoresist layer by adjusting the material properties and rotating speed, among other things.
This example model simulates the thinning of the photoresist layer through 2D axisymmetric modeling, utilizing swirl flow in the Laminar Flow interface and Free Surface feature. The first transient study calculates the variation of photoresist thickness (initial 10 um) within 120 s at 2 mPas and 8000 rpm. The second transient study uses a parametric sweep to calculate the photoresist thickness at different viscosities and speeds.
The results show that:
- The photoresist layer gradually thins as the wafer rotates, and the thickness is consistent with theoretical results (Emslie, Bonner, and Peck Model).
- The smaller the viscosity, the faster the rotational speed, and the thinner the photoresist layer.
Notes:
- Photoresist is treated as a Newtonian fluid without considering shear thinning or thickening effects and the influence of temperature on viscosity. If there is a non-Newtonian effect, a non-Newtonian constitutive should be used.
- The evaporation of photoresist solvent has not been considered. If necessary, the evaporation flux can be added to the flux on the Free Surface feature.
- The nonslip boundary conditions that are used to treat the contact surface between the photoresist and silicon wafer may require the selection of other wall conditions if there is slip behavior.
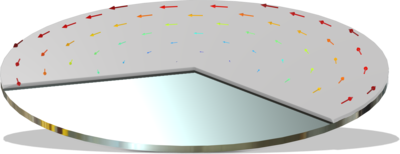
This model example illustrates applications of this type that would nominally be built using the following products:
however, additional products may be required to completely define and model it. Furthermore, this example may also be defined and modeled using components from the following product combinations:
The combination of COMSOL® products required to model your application depends on several factors and may include boundary conditions, material properties, physics interfaces, and part libraries. Particular functionality may be common to several products. To determine the right combination of products for your modeling needs, review the Specification Chart and make use of a free evaluation license. The COMSOL Sales and Support teams are available for answering any questions you may have regarding this.