Topology Optimization of a Step Thrust Bearing
Application ID: 105861
In this tutorial model, a step thrust bearing is topology optimized to maximize the bearing capacity. A step thrust bearing consists of a stepped bearing surface on which the end of the shaft rotates. The entire assembly is submerged in a lubricant. The shaft collar is assumed to be spinning without any axial motion in the bearing.
The model shows that initializing the optimization with a nonuniform design, can result in local minima with a specific number of steps.
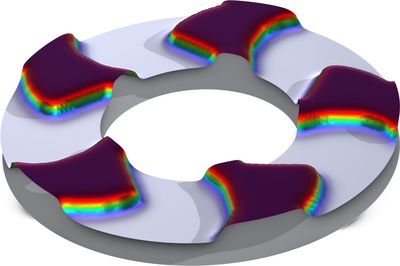
This model example illustrates applications of this type that would nominally be built using the following products:
however, additional products may be required to completely define and model it. Furthermore, this example may also be defined and modeled using components from the following product combinations:
- COMSOL Multiphysics® and
- Optimization Module and
- Rotordynamics Module and
- Structural Mechanics Module
The combination of COMSOL® products required to model your application depends on several factors and may include boundary conditions, material properties, physics interfaces, and part libraries. Particular functionality may be common to several products. To determine the right combination of products for your modeling needs, review the Specification Chart and make use of a free evaluation license. The COMSOL Sales and Support teams are available for answering any questions you may have regarding this.