A Multidisciplinary Approach Towards Low Radar Cross-section Air Intake Duct Design
Stealth technology is one of the important requirements for the next generation (5th Generation) combat aircraft. Most of the stealth aircraft design focuses on low radar signature to reduce the detection possibility. Stealth technology allow the aircraft to enter the enemy territory without being detected by the enemy radars. Across the world, only few successful aircrafts are flying which are stealthier in nature. The stealth aircraft design for RCS reduction depends on the nature of mission. The fighter aircraft which take part in air to air battle (dogfight), is designed for reduced front and back RCS, whereas in bombers design, even side and bottom RCS reductions are also been considered. Cavities such as intake, exhaust, landing gear gates, air breath sensors etc. are one of the main RCS contributors. The best way to reduce RCS is by removing or hiding the RCS contributing components from the enemy radar vicinity. Some of the components which cannot be avoided have to be redesigned for stealth with low radar signatures. As aerospace platforms are always multidisciplinary in nature, the design optimization also should follow an integrated approach to achieve the goal. The integrated approach towards computational fluid dynamics (CFD) with computational electromagnetic (CEM) for the conceptual design and analysis of cavity structure such as intake duct of an aircraft having low radar signature is shown in Figure 1. The design constrains has been calculated based on the Indian Reference Atmospheric (IRA = ISA_SL+15) conditions and S-type duct as shown in Figure 2 [4]. The duct has been designed for subsonic flow condition with 0.8 Mach number. The throat area has been calculated to allow maximum mass flow rate through duct. Accordingly, four designs have been modeled using available CAD tool. The aerodynamic flow analysis has been performed using steady state flow equation solved in 3-D field. In the solver, the flow field parameters have been computed based on Reynolds Averaged Navier Stokes (RANS) equations. Ideal gas flow equation along with SST K-omega turbulence model has been used. The results such as mass flow rate, pressure recovery and total pressure loss coefficient have been estimated at the engine face. Initial radar cross section (RCS) has been estimated using RF and Wave Optics module in COMSOL Multiphysics®. The surface points required for raytracing is obtained from the mesh file generated by COMSOL tool and RCS estimation has been performed using in-house MATLAB® code. From the analysis, it has been observed that straight duct with circular head (Cowl) gives better aerodynamic performance, whereas their radar signature contributions are high. On other hand by applying more curvature in the flow path, brings down the aerodynamic performance but improve the radar signatures for stealth. The intake has been designed to reduce the radar signature by compromising with aerodynamic performance threshold. The modified design mean RCS reduction is about 16.94 dBsm, by compromising with 1.33 percentage of lower pressure recovery across the intake duct.
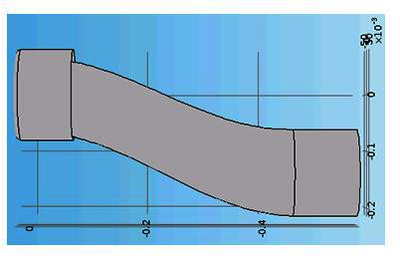
Download
- choudhury_paper.pdf - 0.32MB
- choudhury_abstract.pdf - 0.02MB