Design and Multiphysics Analysis of MEMS Capacitive Microphone
In this paper, design and analysis of a novel MEMS capacitive microphone which uses corrugations and perforations in diaphragm is presented. The corrugation and perforation in diaphragm reduces the residual stress and increases the mechanical sensitivity of diaphragm. Instead of the perforated back plate, holes have been made on the diaphragm. Therefore, potassium hydroxide (KOH) etching can be avoided to make the back chamber and fabrication cost will reduce. The holes in diaphragm reduces air damping in gap. The proposed structure is modeled and studied using COMSOL Multiphysics® software. The analysis results are presented and compared with microphone structure having perforated back plate.
The majority of MEMS microphones use flat diaphragms along with a perforated back plate. The cavity or back chamber is etched into substrate by KOH etching [1]. Cavity forming by KOH etching is a slow and time consuming process. For making holes in back plate, etching is done from the backside in the cavity. The fabrication processes are long and expensive. This complex and expensive fabrication can be avoided by making holes in diaphragm [2], [3].
If air damping is not reduced, it affects the displacement of diaphragm and reduces the sensitivity. A perforation in diaphragm controls the air damping in gap and increases the sensitivity of microphone [4]. In the low pressure range, nonlinearity is caused by diaphragm stress in flat diaphragm [5]. The corrugation technique has been developed to increase linearity of load-deflection behaviour of diaphragm.
The software COMSOL multiphysics® is selected to model and simulate MEMS capacitive microphone. It is a powerful interactive environment for solving problems based on partial differential equations. A 3D model is constructed to describe the operation of microphone. For this work physics chosen is Electromechanics in the Structural Mechanics module. The equations are established by giving suitable boundary conditions.
Figure 1 show the cross sectional view of capacitive microphone with corrugated and perforated diaphragm. Figures 2 and 3 show displacements obtained for the proposed microphone and MEMS capacitive microphone with perforated back plate at pressure 1kPa. Figure 4 shows sensitivity plot of proposed microphone and microphone with perforated back plate.
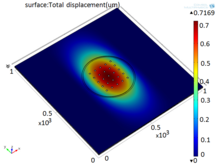
Download
- krishnapriya_poster.pdf - 0.5MB
- krishnapriya_paper.pdf - 0.61MB
- krishnapriya_abstract.pdf - 0.27MB