Flow field analysis of fuel cells to determine temperature distribution and heat dissipation
The increasing demand for more efficient cooling options in the fields of fuel cell mobility and power electronics motivates for the development of novel cooling strategies with improved heat transfer. Forced convection of liquids is a common cooling method and allows high temperature gradients between the heat source and the coolant to be maintained, thus achieving a high heat transfer rate. By using a liquid with a low boiling point, additional thermal energy can be removed from a system by an intended phase transition. With the ambition to increase the lifetime and power density in fuel cell systems, cooling by evaporation is a suitable approach. In this context, the phase transition behaviour into the internal structure of bipolar plates as a central functional element for cooling in a fuel cell must be understood and designed. In this paper, a model geometry for the study of fluid dynamics and temperature distribution in a section of a fuel cell concept, called bipolar plate, is described. Thereby, the paper pursues two different approaches to evaluate the temperature distribution and heat dissipation in these bipolar plates. The first approach is focused on simulating a sequence of 12 periodic cell elements in a row to capture the flow field within the bipolar plate. The cell element is defined by the smallest geometric shape that can be mapped periodically in x-, y-direction to generate the full structure of a bipolar plate flow field. Phase transition of ethanol used as a cooling medium is considered with the aim to represent an evaporative cooling system. Due to the high demand of computational power and memory a second approach was applied, which thematically takes up the COMSOL® blog posts [1, 2] and uses the General Extrusion feature. With this feature, it is possible to map solutions from one domain to the next domain in sequence with the intention to reduce the computational effort. Both described approaches are using the interfaces transport of diluted species (tds), turbulent flow L-VEL (spf), heat transfer in fluids (ht), the chemistry (chem) interface and boundary ODEs and OAEs (bode). With the tds the concentration of the gas phase in the fluid is calculated. The spf is solving for the flow field and the ht for the temperature distribution in the bipolar plate models and chem is implemented to calculate in combination with the chemistry module the material properties of gaseous ethanol. The different approaches are validated and compared to each other to see the benefits and disadvantages with respect to the required computational effort. Finally, flow pattern and temperature distribution provide information about the potential of the regarded cooling strategy and about the layout of the bipolar plate system for effective cooling. The results of the simulations will help to design an efficient evaporative cooling system for high performance fuel cells.
[1] W. Frei, Exploiting Periodicity in Models with High Péclet Numbers. COMSOL®, 2015 [2] W. Frei, Using General Extrusion Operators to Model Periodic Structures. COMSOL®, 2015
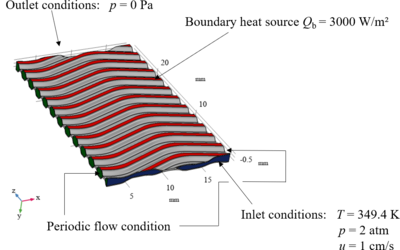