Hydrodynamics and Mass Transfer in Taylor Flow
In the present work, numerical simulations of a Monolith Reactor (MR) are carried out in order to develop a pre-design tool for industrial-scale reactors applied to highly exothermal reactions. The reacting circular channels (2-4 mm internal diameter) are coated with a few micron thick catalytic layer (washcoat), and host a gas-liquid segmented flow (the so-called Taylor flow) known to enhance gas dissolution rates. Therefore the full problem is three-dimensional, locally non-stationary and involves strongly coupled multiphysics phenomena which need descriptions at the washcoat, bubble, channel and reactor scales. The modeling strategy consists in representing each phenomenon with the required level of complexity by progressing step-wise from the local scale to the reactor scale; for that purpose, COMSOL Multiphysics® software is chosen as it allows to couple different physics as well as different scales.
As a first assumption, a uniform temperature is considered for the monolith Aluminum scaffold owing to its high thermal conductivity and to the fast circulation of a coolant fluid in neighbor channels. This allows the use of a single-channel approach to model the reactor. For this model, a typical approach [1,2] used for fully-developed Taylor flow in milli- and micro-channels is chosen, based on the so-called Unit Cell (referred to as UC, see Figure 1): a gas bubble is surrounded by a liquid film and separated by two half liquid slugs, and is represented in a reference frame that is moving with the bubble.
This approach is relevant as long as the considered UC is far enough from the inlet and outlet sections of the channel (0.5 to 1m long). The numerical simulation of liquid-phase hydrodynamics for an isothermal UC is performed in a 2-dimensional representation (axial symmetry). Two simulation strategies are tested: (i) a liquid flowing around a pre-determined bubble-shape object with open inlet and outlet boundaries for the UC, and (ii) a liquid periodic flow in a UC of known pressure drop. The grid is optimized by limiting the maximum and minimum element size near bubble surface and channel wall, and a boundary layer mesh is created close to these boundaries (Figure 2). The grid sensitivity study is performed by varying the number and size of elements and by checking the variation of the calculated pressure drop in the UC.
The pressure and velocity (Figure 3) fields are then used as a numerical “platform” to subtend description of local mass transport phenomena. A fixed concentration is implemented at bubble interface and the chemical reaction is represented via a surface flux boundary condition at the UC wall (neglecting diffusion limitations within the catalytic layer); for mass transport, pseudo-periodicity is considered for the UC. The results allow deconstructing the overall mass transfer flux in the UC for contrasted situations in terms of limiting control conditions (reaction rate slow / fast in comparison with mass transfer). Through this approach gas-liquid mass transfer coefficient (kL) can be estimated for the UC and compared to experimental works and literature values.
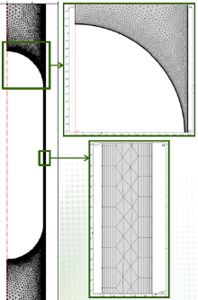
Download
- duran martinez_presentation.pdf - 1.47MB
- duran martinez_abstract.pdf - 0.39MB