Optimization of the acoustic pressure distribution inside a freeze drying chamber
Introduction
The application of power ultrasounds in food dehydration processes have shown a good performance in terms of efficiency, energy reduction and quality of the final product, allowing also a reduction in the convective drying kinetics, and at lower temperatures than conventional air dryers. This sustainable technology needs an airborne power ultrasonic transducer (APUT) to work in a required operational mode at a high power regime in order to generate the desired ultrasonic field inside the dehydration chamber.
The acoustic field generated inside the dehydration chamber depends both on the generator (shape and vibration mode of the radiator); and on the propagation channel (shape, wall material and environmental conditions of the dehydration chamber).
Hence, the analysis and optimization of the acoustic field in the area of interest is essential for and efficient performance in food dehydration processes.
The aim of this work is to present the numerical analysis and optimization and of the ultrasonic field generated by an APUT with stepped circular radiator inside a freeze drying cabinet, using COMSOL Multiphysics®.
Use of COMSOL Multiphysics®
The numerical model, includes the Structural Mechanics Module, the Pressure Acoustics interface and the Multiphysics analysis of COMSOL Multiphysics® 5.3, allowed us to perform the acoustic optimization inside the dehydration chamber.The numerical simulations consider the stepped circular radiator, vibrating in a flexural mode with seven nodal circles at a frequency around 26 kHz, placed inside the drying cabinet. The operational environmental conditions (-12ºC and minimum relative humidity) have been considered for the simulations, as well as the materials of the boundaries of the chamber.
Taking into account the axisymmetric behavior of the stepped circular radiator, the numerical model corresponds to a 2D axisymmetric model, to reduce the computational cost and to permit a refinement of the mesh used in the simulations.
The optimization simulations consist on: firstly, analyze the effects of the side boundaries of the chamber in the pressure distribution in the area of interest; and secondly, determine the most efficient separation between the radiator and the area where food samples are placed. This separation will be determined with a parametric study, in which the location of the radiator changes.
Results
After the parametric analysis, the most efficient configuration relating the radiator and dehydration chamber has been found, by calculating the integrated pressure value in the area where the food samples are placed. This result is presented in Fig.1, with this value for different separation between radiator and samples. The ultrasonic field obtained with this configuration has been validated experimentally.
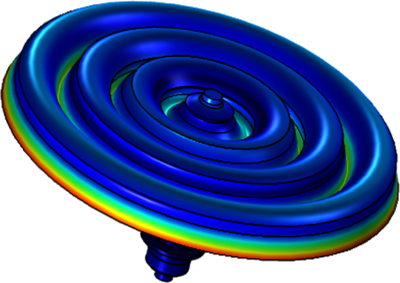
Download
- 2019_COMSOL_Poster_RAG.ppt - 1.09MB
- 2019_COMSOL_Conf_RAG.pdf - 0.73MB