Simulation of Cooling Induced Stress Distribution in Diamond Layer Coating on Steel Tools
Diamond is a modification of carbon and so far the hardest known material. It is well suitable as a protection layer on various materials at high erosive, mechanical or chemical load. CVD diamond coated tools have high wear resistance, tool life, and surface quality. In this research steel is used as tool material since it is easy to manufacture, in comparison to other materials low in price and it has a high strength and toughness. The hot filament chemical vapor deposition process (HF-CVD) was established as the most important diamond coating process for homogeneous coating of tools, for example 3D freeform surfaces or aluminum die-casting tools or other mechanical parts. In the HF-CVD process, a methane-containing hydrogen atmosphere is excited at hot tungsten carbide wires which are heated. During the coating process both materials steel and diamond reach typical temperatures between 750 °C and 950 °C.
There is a major challenge in CVD diamond coating on steel materials that has to be solved. Both materials have very different coefficients of thermal expansion. By cooling from the coating temperature to room temperature different strains and high residual compressive stresses appear in the diamond layer, often causing a spontaneous buckling or spalling of the diamond layer. Investigations aim for a defined surface design that can reduce the generation of residual stresses in the coating.
This paper will describe the setup of simulations for cooling and residual stress analysis in layered materials. Through the use of the simulation software COMSOL Multiphysics®, 2D models were developed to simulate the cooling process of a coated substrate material (AISI 4340) from 800 °C down to 20 °C. For the setup of the models, the physics interface Solid Mechanics, Heat Transport in Solids and the multiphysics coupling Thermal Expansion and Temperature Coupling were used. In the simulations a monolayer of CVD diamond with a thickness of 5 μm is applied on top of the substrate material. For the model a plane stress state is assumed, allowing deformation in all directions. Meshing is done with triangular elements to allow for easy mesh displacement in any direction. The greatest magnitude of main stress was evaluated and displayed in false colors. The negative values represent compressive stresses in the diamond coating. The interface between the substrate and the diamond layer is of particular interest in these simulations to gain more detailed knowledge about excessive compressive stresses within the diamond layer to prevent delamination.
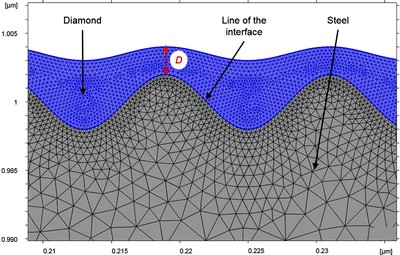