Multistudy Optimization of a Bracket
Application ID: 19761
In this shape optimization example, the mass of a bracket is minimized by changing the size and position of a number of geometrical objects.
The requirements give limits both on the lowest natural frequency, and on the maximum stress in a static load case. This means that results from two different study types must be used as constraints in the optimization problem. For the stress constraint, a maximum over the whole domain must be computed, since the location of the peak stress is unknown.
In addition, several geometrical constraints are required to maintain a feasible geometry.
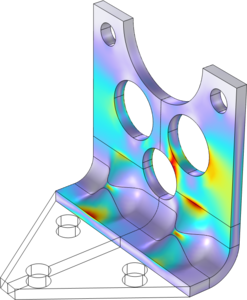
This model example illustrates applications of this type that would nominally be built using the following products:
however, additional products may be required to completely define and model it. Furthermore, this example may also be defined and modeled using components from the following product combinations:
- COMSOL Multiphysics® and
- Design Module and
- Optimization Module and
- either the MEMS Module, Multibody Dynamics Module, or Structural Mechanics Module
The combination of COMSOL® products required to model your application depends on several factors and may include boundary conditions, material properties, physics interfaces, and part libraries. Particular functionality may be common to several products. To determine the right combination of products for your modeling needs, review the Specification Chart and make use of a free evaluation license. The COMSOL Sales and Support teams are available for answering any questions you may have regarding this.