Turbulent Mixing in a Stirred Tank
Application ID: 12727
This example shows how the mixing capability of a stirred vessel can be evaluated. To efficiently reach the steady operational conditions the turbulent flow is solved for using a frozen rotor analysis, and a following time dependent simulation. When a quasi-steady flow field has developed, the turbulent mixing of a trace species is simulated, and the mixing time until it is fully mixed is evaluated.
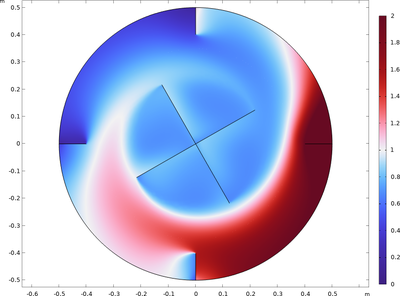
This model example illustrates applications of this type that would nominally be built using the following products:
however, additional products may be required to completely define and model it. Furthermore, this example may also be defined and modeled using components from the following product combinations:
- COMSOL Multiphysics® and
- either the CFD Module, or Heat Transfer Module and
- either the CFD Module, or Polymer Flow Module and
- either the Battery Design Module, CFD Module, Chemical Reaction Engineering Module, Corrosion Module, Electrochemistry Module, Electrodeposition Module, Fuel Cell & Electrolyzer Module, Microfluidics Module, Pipe Flow Module, Porous Media Flow Module, or Subsurface Flow Module
The combination of COMSOL® products required to model your application depends on several factors and may include boundary conditions, material properties, physics interfaces, and part libraries. Particular functionality may be common to several products. To determine the right combination of products for your modeling needs, review the Specification Chart and make use of a free evaluation license. The COMSOL Sales and Support teams are available for answering any questions you may have regarding this.