Metal Processing Module Updates
The Microstructure-Based Phase Transformation Model
A new microstructure-based phase transformation model is available for steel hardening simulations. This transformation model eliminates the need to manually specify the rate coefficient or fit the model to time–temperature-transformation (TTT) data. It builds on the existing Kirkaldy–Venugopalan phase transformation model, which is now referred to as the Kirkaldy–Venugopalan, simplified model. In the Steel Composition node, you can specify the chemical composition, Fe–C diagram, and austenite grain size before selecting the model formulation for use with the Microstructure based phase transformation model.
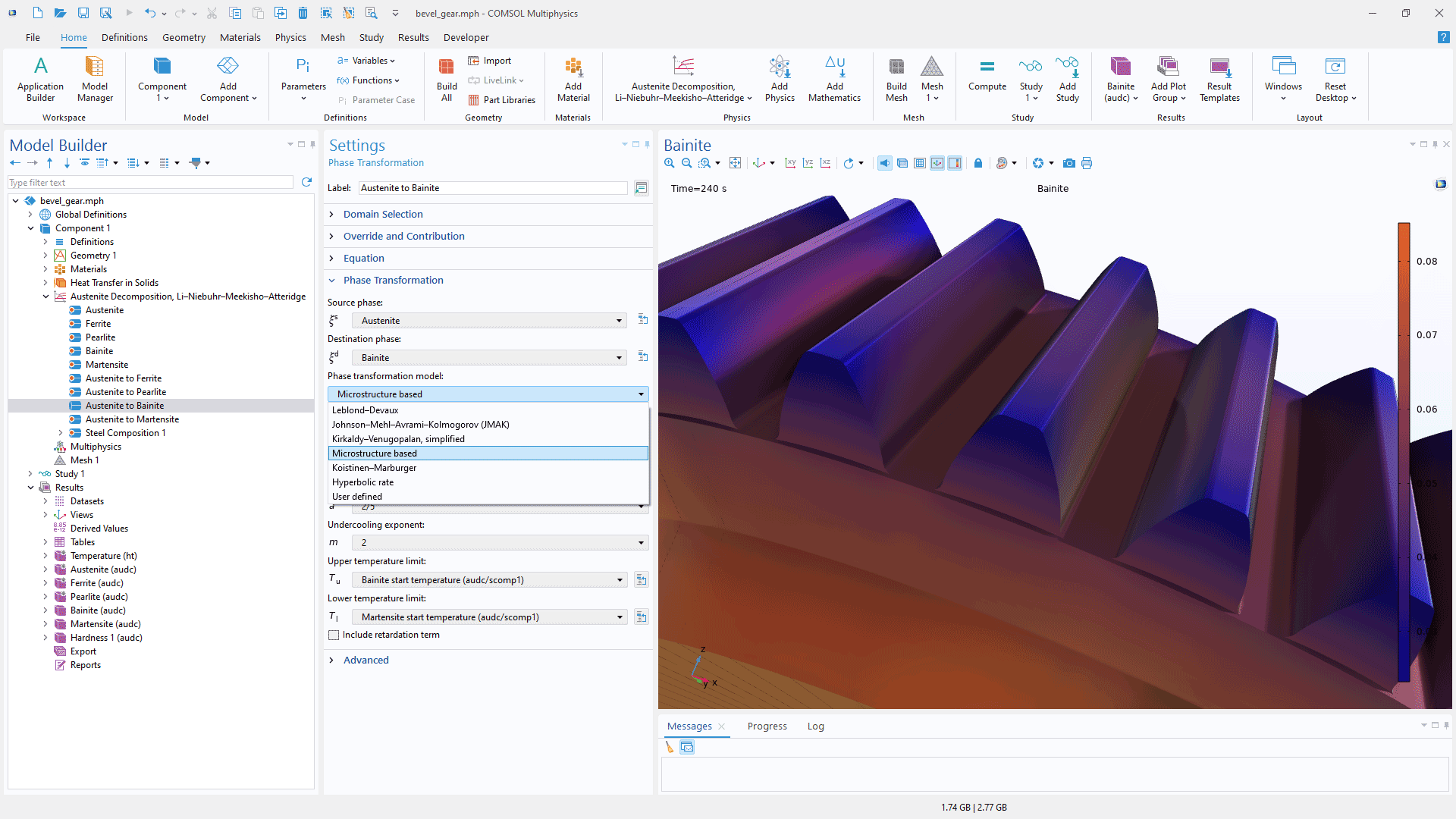
New Interfaces for Austenite Decomposition
Two new interfaces have been added to simulate phase transformations during steel hardening. The Austenite Decomposition, Kirkaldy–Venugopalan and Austenite Decomposition, Li–Niebuhr–Meekisho–Atteridge interfaces automatically configure the features necessary for the respective Kirkaldy–Venugopalan and Li–Niebuhr–Meekisho–Atteridge phase transformation model formulations.
Improvements to the Import From JMatPro®
The import functionality from JMatPro® now includes the ability to use imported phase transformation data without predetermining a specific phase transformation model. For many applications, this improves the quality of phase composition predictions.
Enhanced Thermal Strain and TRIP Strain Modeling
In version 6.3, a new Density based formulation makes it possible to base thermal strain computations on temperature-dependent densities of the different phases. This formulation provides an additional method to, for example, capture the dilatometric response of steel that has undergone a temperature change and phase transformations. Additionally, TRIP coefficients can now be computed by using the relative densities of the phases involved in a phase transformation.
Extension to Hardness Computations
The existing Hardness feature has been extended to include functionality for calculating the Rockwell C hardness (HRC) after quenching. The hardness calculation is based on the computed Vickers hardness (HV).
New Tutorial Models
COMSOL Multiphysics® version 6.3 brings two new tutorial models to the Metal Processing Module.
Dilatometry Curves from CCT
JMatPro is a registered trademark of Sente Software Limited.